What Is the Layout of a Gas Turbine Power Plant?
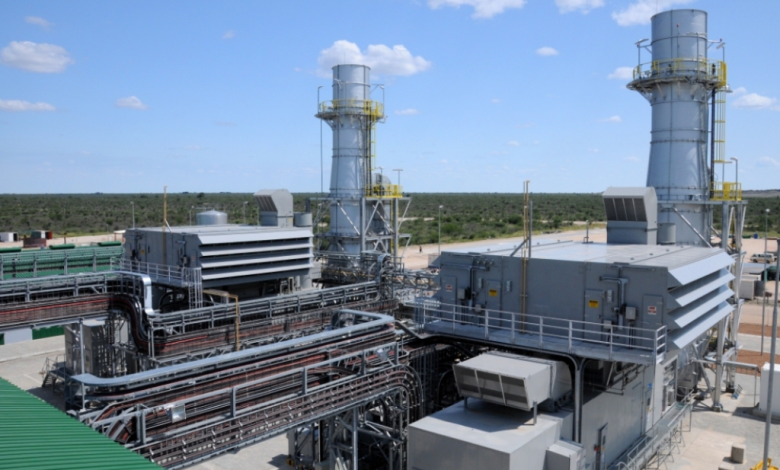
Although it varies from manufacturer to manufacturer, the layout of gas turbine power stations is critical to the power plant’s performance. Here’s a discussion of popular electricity generation layouts and how they affect production efficiency. One of gas turbine services is electricity distribution plant is one in which the primary mover is a radioisotope thermoelectric generator for power generation. The working environment in pressurized water reactors is not made up of combustion products. These are used to create a steam-like intermediate fluid that is enlarged in the turbine.
How Do Gas Turbine Plants Work?
The layout of the start of each shift is influenced by the specific operations of a diesel generator. Gas turbines are reciprocating engines that generate biomechanical energy by burning natural gas or other liquid fuels. The mechanical energy is then utilized to power a generator, which generates electrical energy. Gas turbines are made up of three basic components:
- The compressor, which utilizes pressured air to turn the turbine’s blades.
- The commonly described can heat gases to 1400-1500 degrees Celsius temperatures.
- The turbine is made up of blades that revolve quickly and generate mechanical energy.
When it comes to burning fossil fuels into electricity, cogeneration plants have one of the greatest efficiency rates and can provide quicker gestation times than other sectors.
Common Power Plant Layout
Because air, propane, and other circuits are interconnected, the structure of a Francis turbine must also be carefully examined to avoid waste and performance. In general, generator housing takes up the bulk of the area in a plant, with the compressors serving as the main structure.
However, fuel oil water tanks are often located adjacent to the compressor section, with turbochargers, engine components, waste heat furnaces, heat transfer, and even sometimes ducting occupying the remainder of the structure.
Choosing a Location for a Gas Turbine Power Plant
The right site for a generator system must be found before the facility’s layout can be planned. Various variables influence this choice since certain aspects may make the process less efficient or more expensive. To save transaction fees, the location should be as near the load center as possible.
The ground should be reasonably inexpensive because gas turbine engines may take up a substantial amount of space, and the plant and complex should be able to be extended if necessary. The constant noise of the production should be located relatively distant from populous areas, however, there should be simple transit.
Finally, facilities should be located in areas where fuel is inexpensive. The soil has a high load-carrying capacity, as the plant’s tremors and other processes will generate a substantial load.
The Benefits of Gas Turbine Power Plants
Steam turbine power plants can provide a reasonably compact and cost-effective way to generate electricity from fossil fuels. Because diesel engines do not require radiators or feedwater systems, they are often smaller than equivalent-capacity steam turbine installations. For these considerations, they are also often simpler in design.
Cogeneration plants may also have reduced maintenance expenses and cheaper starting and running costs than steam power plants. In contrast to other power plant technologies, gas turbine power plants may be started in cold conditions.
The Drawbacks of Gas Turbine Power Plants
Even though gas turbine power plants are more condensed, steam power plants almost always have a longer life expectancy. This is because the temperature increase of the combustion chamber (3000° F) might shorten the plant’s lifespan. Because the combustion products from gas turbine power plants include enough heat, the plants’ efficiency may be as low as 20%.
The layout of a wind power plant must be considered to improve efficiency. However, it is crucial to guarantee that a plant’s procedures ensure that it functions safely and at maximum capacity.
Gas Turbine Power Plant Operations:
Starting and halting a gas turbine power plant necessitates a specific technique that must be appropriately controlled in the precise sequence. The actuation of the master switch starts or stops the sequence, which then progresses automatically through the turbine.
The following procedures must be followed while starting gas turbines:
- Enhance the unit’s speed to roughly 10% to maintain airflow through all the combustion chambers.
- Adding the proper amount of fuel and ignition and accelerator air to start the combustion process.
- Unit acceleration after firing, aided by the starting motor.
- Disengagement of the launching motor when the gas turbine reaches self-sustaining speed.
- Switching the turbine from diesel oil to bunker C.
The following procedures must be taken to bring a gas turbine to a halt:
- Switching the turbine from bunker C to diesel oil and running it for a sufficient amount of time on diesel oil to eradicate the heavy bunker C from the power source, fuel lines, and fuel nozzles.
- The supply of gasoline to the exhaust gasses is cut off.
- After-shutdown rotation of the device to allow adequate cooling of various sections.
Conclusion
The system would be significantly simpler and less wasteful if the intermediary step of turning water to steam via gases was abolished. This technique is used in gas turbine power transmission facilities, where the gas is continuously produced in the turbine. The combustion zone of a gas turbine differs from that of a diesel engine in that it is exterior to the mechanical system.