How to Use Diamond Abrasives for Wafer Grinding
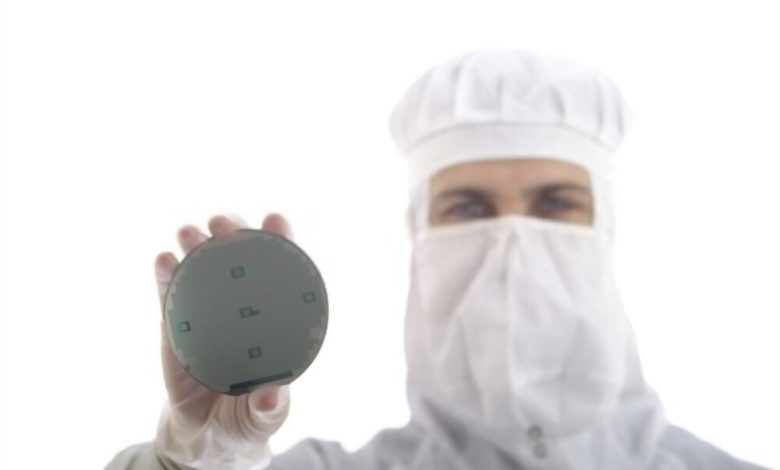
A wide variety of abrasive materials are available for wafer grinding. Read this article to find out more about these materials and other advantages. In addition, you can also check out the KINIK wafer grinding wheels review. We’ll help you make the right choice for your application.
KINIK wafer grinding wheels
The Wafer Grinding Wheel market report provides an in-depth analysis of the market, its revenue forecasts, and competitive landscape. This report analyzes the market size and trends, as well as the key factors driving or inhibiting growth. It presents the key players operating in the market, as well as their latest developments and business strategies. It also provides a SWOT analysis of the leading players in the market, as well as the growth rate of the industry.
The KINIK COMPANY is a Taiwan-based manufacturer of diamond tools and traditional grinding wheels. These include semiconductor dressing, IC production, and stone processing. Kinik also produces a variety of backside grinding wheels and dicing blades. While the company primarily produces diamond tools, it also manufactures reclaimed wafers and monitor wafters.
This process lowers the strained thickness of the surface while minimizing chemical contamination. This process is leading-edge for high-precious reclaimed wafers. The 12-inch KINIK wafer regeneration process has gained huge domestic and international demand. In addition to the advanced technology that these grinding wheels can provide, KINIK is also committed to providing excellent customer service.
In-process dressing of KINIK wafer grinding wheels is another important factor in improving the quality of the finished product. This technology allows a machine to achieve sub-nanometer surface roughness while eliminating the need for post-process finishing operations. Different researchers have studied this method for several years. Continuous anodic dissolution ensures sharp cutting grits while a soft anodic oxide layer reduces the amount of force required for grinding.
Diamond abrasives
Here are some tips to use these materials properly. The grinding wheel 34 is a rotating member that rotates in a chuck table. The abrasive members 341 come in contact with the back side W2 of the wafer during grinding. The process produces a strain layer 10 on the back side of the wafer, which makes the final wafers very smooth.
Fixed abrasive wheels are a popular choice for high-quality wafer grinding. Abrasive quality, cutting edge distribution, and grinding force all affect the quality of the wafer surface. This study aimed to understand the dynamic behavior of diamond abrasives when used for wafer grinding.
CMP (conventional) grinding processes have many drawbacks. While the free abrasive process produces very good surface quality, it has a low efficiency and takes much longer than other processes. Furthermore, the slurry generated during the grinding process can become uncontrollable, resulting in an unstable surface profile and waste. The best choice for diamond abrasives for wafer grinding is one that can meet all the requirements of the manufacturing process.
Polyvinyl alcohol is a natural abrasive that enhances the plastic deformation ability of phenolic resin. Polyvinyl alcohol is easy to crosslink, and it forms a gel under the right conditions. The sol-gel process reduces the bonding bridge between the diamond abrasive grains and the abrasive wheel, resulting in a more uniform surface hardness.
Customized vitrified bond
A customized vitrified bond is an abrasive product made of green body, superabrasive grit, and binder. The pore size can be less than 800 mm. Approximately 70 percent of the pores will have a diameter of between 40 and 500 mm, and the aspect ratio will be greater than 1.2. This process can produce superabrasive particles that are ideal for the grind of wafers.
A custom-designed vitrified bond for abrasive product provides an excellent blend of performance and value. The abrasive is capable of back grinding wafers with an average surface roughness of 35 Angstroms. The combination of a superabrasive component and vitrified bond allows the product to define pores with a diameter of 800 mm or less. Customized vitrified bond for wafer grinding helps to avoid the potential contamination of silicon or electronic components.
A custom vitrified bond provides the highest levels of abrasive performance and flatness. Its advantages over other types of abrasive wheels include longer life and better abrasive particle size. Customized vitrified bond is the most durable and versatile and is easy to control for flatness. These custom wheels are also used in foundry and metal fabrication applications. You can get a free quote from a certified supplier today.
In addition to providing customized grinding wheels, Meister Abrasives has a long history of developing grinding wheels. Meister continuously solicits customer feedback to develop customized solutions. Meister’s state-of-the-art test center helps Meister fine-tune its approach for the best possible results. A customized vitrified bond wheel is the perfect solution for many types of grinding needs. It increases productivity and reduces machining costs.
Click here to read more: https://www.stealthdicing.com/about-gdsi/
Unique porous microstructure
A novel microfabrication technology, PowderMEMS, allows for the integration of multiple BEOL compatible 3D microstructures. This technology is suitable for a wide range of microsystems and can be tailored for various functions. A new characterization technique enables the manufacture of microstructures with high mechanical properties. The advantages of this technology make it ideal for many applications in the semiconductor industry. Here, we examine how the unique porous microstructure is created.
To manufacture unique porous microstructures, a high-temperature annealing process is used. This process makes the silicon surface extremely rough, and the resulting porous microstructure is unique in its appearance. The resulting wafer contains more defects and unwanted impurities than conventional silicon. In contrast, a more conventional process, which requires a high-temperature annealing cycle, generates a uniform layer with a single layer of silicon.
Another new technology is the use of a double cell. A double cell is a microstructure made of two half-cells separated by a silicon wafer. The silicon wafer acts as the anode and cathode. The electrolyte flows from one half-cell to the other through the silicon wafer, making the back-side the local cathode and front-side the anode.
Researchers studied the effectiveness of the new technology by using the data gathered from a 200-mm back-ground wafer. The new method enables the analysis of warpage, waviness, and roughness from the edge area to the center. The researchers expect this method to become a standard technology in the near future. And they believe that it is worth exploring. Its potential is enormous. It has already made it possible for a broad range of applications, including precision wafer grinding, semiconductor manufacturing, and advanced optical technology.
While traditional silicon nanoparticles are very large, the size of the pores is small. This means that they cannot be effectively analyzed by conventional etching methods. The unique porous microstructures used in wafer grinding have very low adhesion. The porous microstructures are also more resistant to HF based processes, and are suitable for precision grinding applications. This is why they are so valuable.
Thanks for visiting wizarticle