Financial Impact of System Downtime and How Control Integrators Reduce Risk
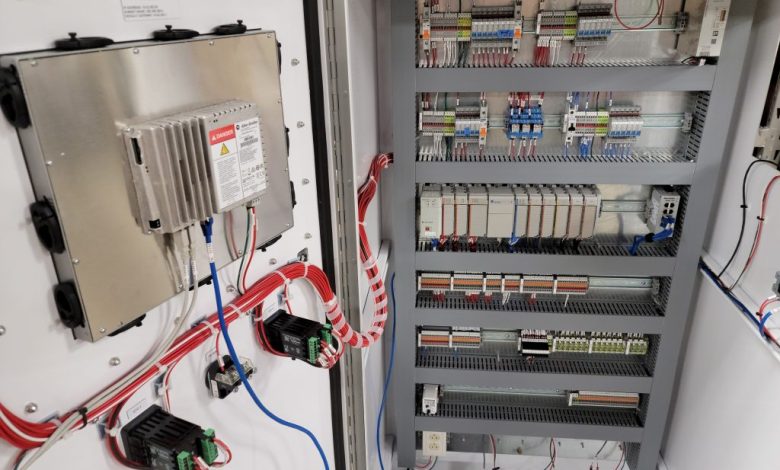
System downtime is more than just an inconvenience; it can lead to significant financial losses for businesses across industries. Whether it’s manufacturing, logistics, or any other sector relying on continuous operations, even a short period of downtime can snowball into larger issues. While many companies may focus on getting systems back online, it’s crucial to understand the full financial impact of downtime and how working with a controls integrator can mitigate these risks effectively. Let’s break down the various ways downtime can affect your bottom line and why control integration is key to minimizing these effects.
Analyzing Lost Production Output and Its Revenue Impact
When systems go offline, one of the most immediate consequences is the halt in production. Every minute that machines aren’t running is a minute of lost output, which directly translates to a loss in potential revenue. For industries that operate on tight schedules, even a small disruption can lead to significant delays in meeting demand. The financial loss isn’t just about the immediate downtime—there’s often a ripple effect that impacts future orders as well.
This is where a controls integrator can make a substantial difference. By designing and implementing automated systems that are robust and less prone to failure, businesses can minimize downtime and maintain consistent production levels. These specialists ensure that your systems are optimized for maximum uptime, helping you avoid the costly interruptions that can eat into your revenue.
Evaluating Increased Operational Costs Due to Inefficiencies
When systems go down, inefficiencies tend to creep in. Without automation running smoothly, manual processes may have to take over, and that often leads to mistakes or slower operations. As a result, operational costs start to rise. Whether it’s wasted energy, increased resource use, or the need for additional temporary labor, the expenses add up quickly.
Control integration plays a critical role in streamlining these processes and reducing inefficiencies. A skilled controls integrator designs systems that keep everything running smoothly and minimize the need for manual intervention. By integrating more efficient processes, businesses can reduce the operational costs that are often associated with downtime and maintain a higher level of productivity.
Assessing Labor Costs from Idle Time During System Failures
One of the less obvious but significant costs of downtime comes from labor. When machines stop working, employees who are supposed to operate those systems are often left idle. Workers may be standing by, waiting for the systems to come back online, which translates into paying wages without receiving any output in return. Over time, this idle time can represent a substantial financial loss.
Control integrators can reduce these idle periods by implementing solutions that allow for quicker system recovery and minimal disruption. Additionally, having a more reliable system in place reduces the frequency of downtime, which means employees can spend more time working productively. By preventing unnecessary idle time, businesses can save on labor costs and maintain higher levels of efficiency during working hours.
Measuring Delays in Order Fulfillment and Customer Dissatisfaction
Downtime doesn’t just affect internal operations; it can also lead to delays in fulfilling customer orders. In today’s fast-paced business environment, customers expect on-time delivery, and any delays can lead to dissatisfaction or even lost business. When orders are delayed due to system failures, customers may choose to take their business elsewhere, causing a long-term revenue loss.
By partnering with a controls integrator, businesses can implement more reliable and efficient systems that reduce the likelihood of these order delays. Control integration ensures that all aspects of the production process work together seamlessly, allowing companies to meet their customer commitments and avoid the reputational damage caused by late deliveries. A well-maintained, automated system helps businesses keep their promises to customers, ultimately protecting both revenue and customer relationships.
Calculating the Financial Strain of Emergency Repairs and Replacements
When systems fail, it often leads to unexpected costs in the form of emergency repairs or even replacements of critical machinery. These repair costs can be significantly higher than the routine maintenance that would have prevented the issue in the first place. Worse, if key components need to be replaced, the expenses can skyrocket, and the extended downtime adds to the financial strain.
A controls integrator can help businesses implement preventive maintenance strategies, reducing the likelihood of catastrophic system failures. Through proper control integration, businesses can better monitor the health of their systems and address potential issues before they result in expensive repairs or replacements. By reducing the need for emergency fixes, companies can save money and extend the lifespan of their equipment.
Reviewing Long-term Depreciation and Wear from Unplanned Downtime
Unplanned downtime not only disrupts immediate operations but can also accelerate the depreciation of machinery. When systems are frequently halted and restarted, it places more wear and tear on the equipment, reducing its overall lifespan. Over time, this leads to a faster depreciation of assets, requiring businesses to invest in new equipment sooner than expected.
Working with a controls integrator allows businesses to implement systems that are less prone to breakdowns, reducing the stress placed on machines. With proper control integration, companies can maintain a more consistent operational pace, preventing the kind of excessive wear that leads to premature equipment failure. By extending the life of their machinery, businesses can delay costly capital expenditures and better manage their financial resources in the long term.